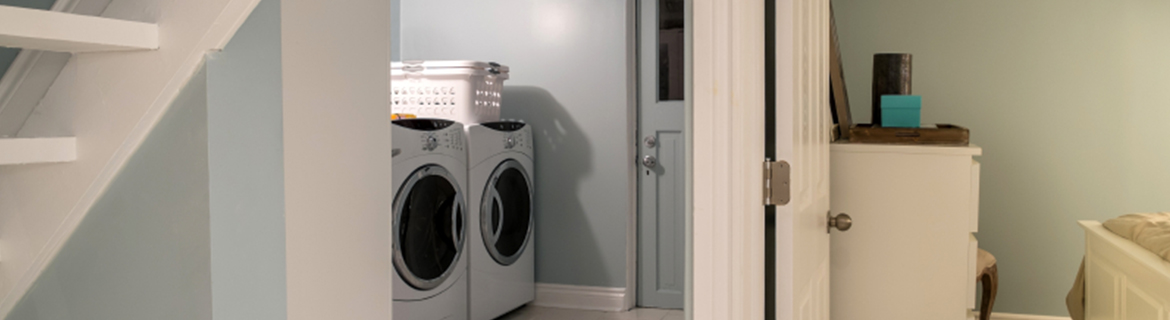
A Basement Finishing ℞
You have many weapons to fight moisture damage, from passive exterior applications like house wrap and attic/roof ventilation to active drying solutions like bathroom exhaust fans and even whole house air exchangers.
No builder can guarantee complete moisture protection. The exterior assault from Mother Nature is unstoppable. But the interior battering can be just as ferocious. A family of four generates water vapor from all their activities, including showering, cooking, bathing, washing, etc. It adds up to an estimated 13 gallons each week (after converting the mass of water vapor to an equivalent volume of liquid water).
Because you build a great home, observe code, and make smart choices about best practice, the home’s passive and active drying systems keep moisture-loving mold and mildew safely at bay.
Then, for many builders, there’s the basement.
Your approach to exterior moisture control probably includes a rigid foam board cladding around the exterior. It makes sense for a couple reasons. First, the thin, light, and nearly impervious rigid foam board shields the foundation wall from wintry temperature extremes, when the concrete can act as a gigantic, whole-house thermal break.
The proven high-R properties of extruded polystyrene (XPS) can mitigate the transfer, helping provide an extra measure of household comfort on a cold January evening.
Second, rigid foam board helps backstop the waterproofing compound applied to the concrete. An XPS foam board, for example, is ASTM C272-rated to be 99.7 percent waterproof by volume.
The tricky part isn’t the exterior sub-grade. It’s the interior, especially if the owner has specified a finished basement.
A concrete basement wall is packed with water and will be shedding it for years as water vapor. As one basement finisher observes, “Every basement is susceptible to water … it’s only a matter of time.” If provision isn’t made to account for concrete ‘off-vaporing,’ the drywall and framing stands very little chance from moisture-induced mold, mildew, and/or rot.
A basement wall system should not be constructed the same way as an above-grade wall system. It should be engineered for moisture-prevalent, below-grade conditions. Colder basement walls (structural elements are in direct contact with the ground) should be insulated with non-water sensitive insulation such as rigid insulation or semi rigid insulation to minimize condensation from warmer moist interior air, especially in summer. For an in-depth guide to basement finishing best practice, visit here and review pages 12-14.
Experts say a basement finishing system should offer homeowners:
Traditional paper-faced gypsum board wall systems fall short in meeting all seven. Today more and more homebuilders, home remodelers, and homeowners specify systems like the Owens Corning® Basement Finishing SystemTM. This engineered, basement-friendly finishing solution has proven to deliver the long-term peace of mind contractors and homeowners expect. To learn more, visit here.