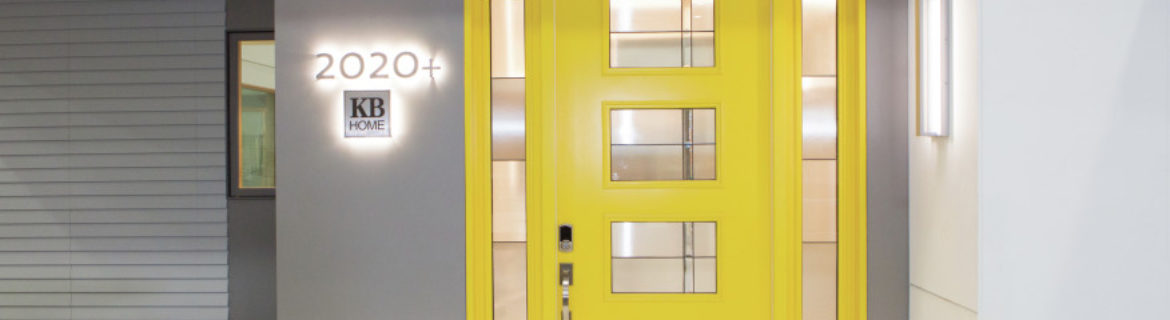
It’s no secret that innovation happens at a snail’s pace in the home building business. Builders and manufacturers independently explore new ideas but keep progress under wraps in order to maintain a competitive edge. This means that game-changing concepts, new products, and innovative technologies are rarely shared across the industry.
The Greenbuild KB Home ProjeKt team broke down these barriers and tapped into the combined brainpower of one of the country’s largest builders, world-class manufacturers, and leading-edge experts in an unprecedented spirit of collaboration, even among competing brands. The result is nothing short of groundbreaking: The demonstration home, on display Oct. 5-7 at the 2016 Greenbuild International Conference and Expo in Los Angeles, will take attendees on a time-travel look at best practices in home building now, in 2020, and in 2050.
2016 Greenbuild KB Home ProjeKt
ProjeKt’s multifaceted team is made up of forward-looking organizations from business, design, and academia, including Whirlpool, Owens Corning, Kohler, Sherwin-Williams, Savant, KTGY Architecture + Planning, Virginia Tech, and a range of other partners and sponsors. The group’s broad expertise in a variety of key disciplines meant it was able to generate and develop innovative but practical ideas about the future of home building, says Dan Bridleman, senior vice president of sustainability for Los Angeles–based KB Home, the No. 6 builder on this year’s BUILDER 100.
“We felt it would be important to demonstrate not what you could do today, not what you could in 2020, but to bring a collaborative group of our partners together with some big thinkers and demonstrate what could be,” says Bridleman. “Utilizing collaboration as a new mode of development, this group of thought leaders has been able to leverage their collective vision and expertise into something greater than could have been conceived of by any individual organization.”
THE PROCESS
In a series of summit meetings earlier this year, project participants were challenged to predict future trends and invent solutions to problems that don’t exist yet. They vetted every aspect of the 2,100-square-foot home for its importance (or lack of importance) in coming years. For instance, the garageless floor plan is a nod to the growth of the sharing economy. In a community of the future, not every homeowner will have a car, experts say; many will share one with neighbors, use a ride-sharing service, or rely on driverless car systems.
The home’s modern design is geared to attract young home buyers who have grown up in the digital age. “The architecture of the home is quite a bit more contemporary than a typical production house, but the next generation of first-time buyers is into contemporary design because it’s what they’ve had in their urban apartments and on their Apple phone and iPads—a sleek, contemporary look,” says KTGY principal Manny Gonzalez, the project’s lead architect.
KTGY’s open, one-level layout takes the flex space of today to a Jestons-like level with a main room that can be reconfigured within minutes for different purposes. A cartridge wall in the secondary bedroom contains a fold-up bed and fold-down desk, allowing it to function as an office or bedroom. The wall can also move out of the way to expand the adjoining great room, and a video screen rotates to allow either room to use it. The cartridge concept, developed by Virginia Tech’s Center for Design Research, is “a new way of building architecture” that utilizes robotics to create house parts, much like an automotive assembly line, says Joseph Wheeler, co-director of the center. (Click here for more about the cartridges.)
HIGH PERFORMANCE
One of the main goals of the project is to demonstrate a future home’s potential for higher levels of performance without increasing costs. “We are going beyond code compliance and even beyond what we would call Sustainability 2.0,” says Jacob Atalla, KB Home vice president of sustainability. “In thinking about the future, we’re talking about restorative design—design that gives back to the environment.”
To that end, the home boasts massive amounts of insulation and can accept plentiful solar panels to meet California’s Title 24, which requires that all homes produce as much energy as they use by 2020. A high-performance wall assembly will help mitigate heating and cooling loads and keep occupants comfortable no matter the region or climate. Thermos-like vacuum insulation panels from Owens Corning work with blown-in insulation, Owens Corning’s Foamular XPS rigid foam insulation, LP sheathing, Tyvek housewrap, and James Hardie siding for an R value of 40. The LP OSB sheathing is treated with the company’s fire-rated Flame Block material, unheard of in today’s single-family residential construction. In addition, a Tesla Powerwall battery will store extra solar energy, providing peace of mind in the case of a weather event or other disaster.
“When a structure like the KB Home ProjeKt strives for net zero energy, it’s not just the insulation or the housewrap or the mechanical systems alone, it’s how they all work together to create a home that delivers the results that have the least impact on the environment and the pocketbook,” explains Gonzalez.
In another example of collaborative ingenuity, the wall assembly also includes Polyguard’s non-chemical TERM system that provides protection from moisture, water, and energy leaks as well as pests such as termites.
“Together, this team pushed the envelope of building science to literally go where no one has gone before in the application of integrated building science,” says David Rosebery, Owens Corning business marketing leader for residential insulation. “What we’ve been able to prove is that building sustainable, code-compliant, comfort-driven homes can be achievable and affordable for builders while delivering a new standard of comfort and performance for the homeowner.”
GREEN FEATURES
Without a doubt, the home of the future will be technology based, and the ProjeKt house demonstrates how manufacturer collaboration will drive it forward. A Savant Pro smart home system combines climate, lighting, entertainment, and security functions in a single interface with a voice-activated remote control. In addition, Schneider Electric will demonstrate a next-generation energy management system that can pinpoint energy use down to the individual circuit breaker and alert the homeowner when irregular usage occurs. Lutron’s wireless system allows homeowners to program lights and shades to turn on or off at a set time every day, and it will automatically adjust as the seasons change.
Water conservation is a crucial component of the home, met by state-of-the-art products such as Kohler low-flow faucets and showerheads and dual-flush toilets, Rain Bird weather-based irrigation, and a device that shows residents how much water they’re using every day. A KitchenAid dishwasher recycles water from the final rinse cycle and saves it for the next load’s pre-rinse, using 33% less water than a traditional unit. If built on site, the home also would be equipped with graywater recycling and rainwater management features, Atalla adds.
A focus on homeowner health is met by Cradle to Cradle–certified products and materials, air-quality sensors, Shaw Floors waterproof carpeting, lighting that enhances residents’ Circadian rhythms, and zero-VOC Sherwin-Williams paint with formaldehyde-reducing properties. Sherwin-Williams’ Paint Shield, a coating that the manufacturer says kills 99.9% of common bacteria within two hours on a painted surface, will also be on display.
A Carrier air purifier will kill airborne pathogens such as bacteria, viruses, and mold, and the company’s energy-recovery ventilator will maintain a blend of fresh outdoor air and conditioned indoor air.
The home’s interplay of products and materials will help it weather whatever Mother Nature might have in store for years to come, adds Atalla. “We’re layering two or more systems in the same assembly to create something that’s more resilient and durable, which may be needed as the climate changes,” he says.
While some might question the use of redundant materials and overlapping systems, the project team wanted to provide abundant efficiency, durability, and comfort for future industry pros to build on. “What we’re doing today might be adding layers of cost that someone could think is unnecessary, but in the future when industry experts collaborate together across companies, they’ll be able to find better economies of scale,” Atalla explains. “Our team for this house doesn’t have all the answers, in fact, this home is just the beginning of thinking about new ways of building.”
Click here for a virtual tour of the Greenbuild KB Home ProeKt.